Boat Building in "Balsa Core"
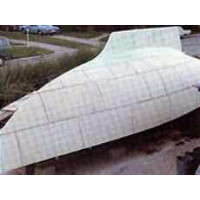
Balsa Sandwich Technique involves the use of a frame and batten mould and balsa sheets of approximately 1’6" x 3’ are sewn into the mould. The outer skin is laid up over this. The balsa comes in approximately 2" square blocks which are glued onto a scrim to make up the 1’6" x 3’ panel.The balsa is quite flexible and lays around most compound curves without giving any unfair surface.In general balsa is limited to use above the water line although we do extend the balsa down to the cabin sole,cheap foam is used during the laying up stage and this is later removed from the inside to give a single skin area below the cabin sole and down into the keel where the floor will be bonded in.
Balsa sandwich generally is made up in 3/8", �" or �" thicknesses. It can also be two layers of 3/8" with a layer of chopped strand mat between the layers of balsa. This double balsa technique provides an extremely strong and stiff hull, however, the technique is a little more expensive than using the single layer of balsa. The inner skin on a balsa sandwich vessel usually is one third of the thickness of the outer skin. Balanced laminates can be used but we feel that the extra laminate on the outside is required to provide the necessary impact strength. Although a balanced laminate of 50% of the weight of the inner and outer skins would give a better structural result, one has to think of the impact strength as this is quite an important matter with a cruising vessel.
As mentioned before the first step is building the mould. How to is described step by step in the plans. The materials for the mould are quite inexpensive and second hand timbers are ideal for this purpose. If your lucky someone nearby will be inspired by your efforts and purchase the mould of you when you've finished to build his own boat allowing you to recover some of your costs. When the mould is finished the foam or balsa is attached via stitching , toggling or nailing. The outer laminations of fiberglass and resin, as per the specification in your plan, are then applied. The hull, with the mould inside, is then rolled over and set up in a suitable cradle after which the mould is then lifted out of the hull and once again recycled as internal fitout material or sold to another builder.
After the hull shell has been trued up and the sheer line faired with battens the next stage is to cut channels through the core in certain stress areas. These areas are shown clearly in the plans. Reinforcing strips of extra fiberglass are layered in these areas attaching to the outer skin. The whole of the interior is now laminated with the inner layers of fiberglass. Bulkheads and solid floors are now installed as per the plans. You can how proceed to start on the interior fitout.